The EMF-EMFL Range: High Shear Bottom Tank Emulsifiers
The industrial emulsifiers in our range are meticulously designed to have a robust and durable structure, aimed at achieving a seamless integration between the rotor and stator, ensuring that both components remain perfectly concentric.
This strategic design prevents any misalignment that could arise during various stages of the manufacturing process, promoting efficiency and precision in each operation.
As for the sealing system, a double-cartridge model has been chosen. This detail not only ensures impeccable sealing, eliminating the risk of leaks or contamination but also greatly facilitates assembly and disassembly tasks.
In this way, valuable time is saved, and maintenance and adjustment procedures are simplified, allowing for greater agility and flexibility in managing production processes.
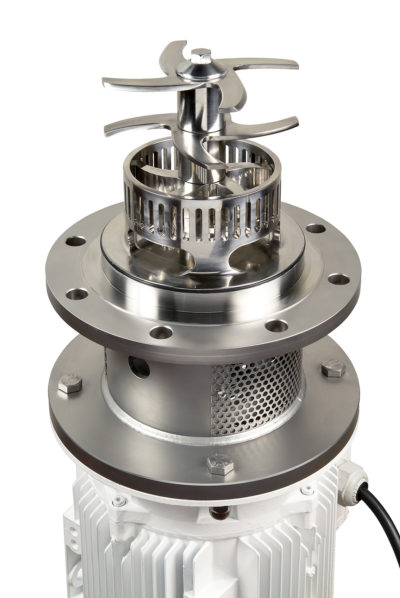
The versatility of these industrial emulsifiers is remarkable. They can operate efficiently in both open tanks and closed vessels and are compatible with atmospheric, pressurized, or vacuum conditions. This adaptability makes them ideal for a wide range of applications and industrial sectors, allowing them to seamlessly integrate into different production lines.
Additionally, these units are specially designed to work optimally with anchor-type agitators or propellers designed to promote homogenization. This synergy between components maximizes the overall system performance and ensures the production of final products of the highest quality and consistency.
Every detail of our industrial emulsifiers has been conceived to meet the highest demands of the industrial sector, providing concrete and effective solutions to the everyday challenges faced by industry professionals. The combination of robustness, precision, versatility, and compatibility with other equipment positions them as a preferred choice for companies looking to elevate their production standards and operational efficiency.
How do these machines work, and what are the industrial processes that occur inside the tank?
Industrial emulsifiers EMF-EMFL, strategically installed at the bottom of the tank, play a crucial role in the process of dissolving heavier particles, standing out for their exceptional effectiveness in this crucial aspect of the emulsifying process. This optimized location is what allows these machines to effectively deal with denser particles, ensuring complete and uniform integration of all components of the mixture.
The operating mechanics of these emulsifiers are as fascinating as they are efficient. The turbine, as it rotates, generates the necessary suction to direct the fluid towards the center of the head.
Here, centrifugal force comes into action, propelling the fluid towards the periphery of the rotor. It is in the intermediate space between the turbine and the stator where the product experiences high pressure, leading to a detailed and thorough grinding process.
Subsequently, the product is directed through the openings in the head, and it is here that the high rotational speed produces intensive shearing force, promoting the dispersion, emulsification, and ultimately, the homogenization of the mixture. This shearing force, synonymous with high precision and refinement, is responsible for breaking down and evenly distributing each element within the final compound.
The combination of high shear rate and the variety of available heads – whether perforated, slotted, or screened – results in the creation of particles of the ideal size, which is crucial for achieving stable emulsions and mixtures with an exceptional level of homogeneity. Each head is meticulously selected based on the nature of the process, ensuring optimal results tailored to the specific needs of each industrial application.
This meticulous and detailed procedure that occurs within the tank is what guarantees the attainment of final products of unparalleled quality, characterized by their consistency, stability, and homogeneity. Each phase of the process is monitored and controlled with precision, ensuring that each particle, regardless of its weight and size, is processed uniformly and thoroughly, thus contributing to the creation of final products of a superior quality standard.
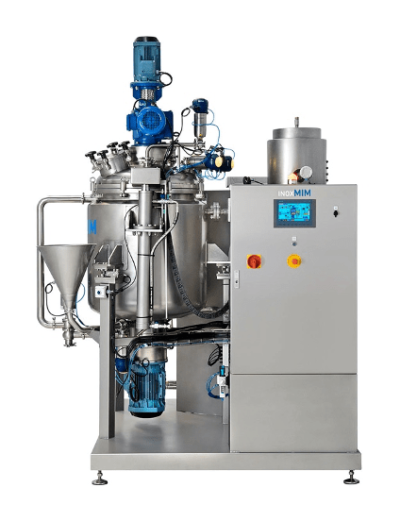
Bottom emulsifier for creams
In conclusion, the technical sophistication and operational precision of the EMF-EMFL industrial emulsifiers, combined with their strategic design and ability to adapt to various requirements, make them indispensable allies in the pursuit of excellence in the field of industrial emulsification and mixing. The detailed nature of the processes that take place inside these tanks reflects InoxMIM’s dedication and commitment to innovation and quality, providing solutions that elevate industry standards.
Some of our emulsifiers:
Contact us to resolve any questions
At InoxMIM, we understand that every production process is unique and demands customized solutions. Our industrial emulsifiers are designed to elevate your production standards and take you to a new level of excellence. Ready to transform your production line and conquer the market with superior quality products?
Don’t wait any longer! Contact us today and discover how our technological innovations can propel your business. Whether you need technical advice, a quote, or assistance with implementation, our team of experts is ready to guide you every step of the way. Explore the world of possibilities that InoxMIM can unlock and take a leap into the future of the industry by choosing our machinery.
Call us at 972 58 20 40 or email us at info@inoxmim.com to begin your journey toward industrial innovation with InoxMIM. Secure the future of your production with our state-of-the-art emulsifiers and become a pioneer in industrial excellence!